Where are the Cost Savings?
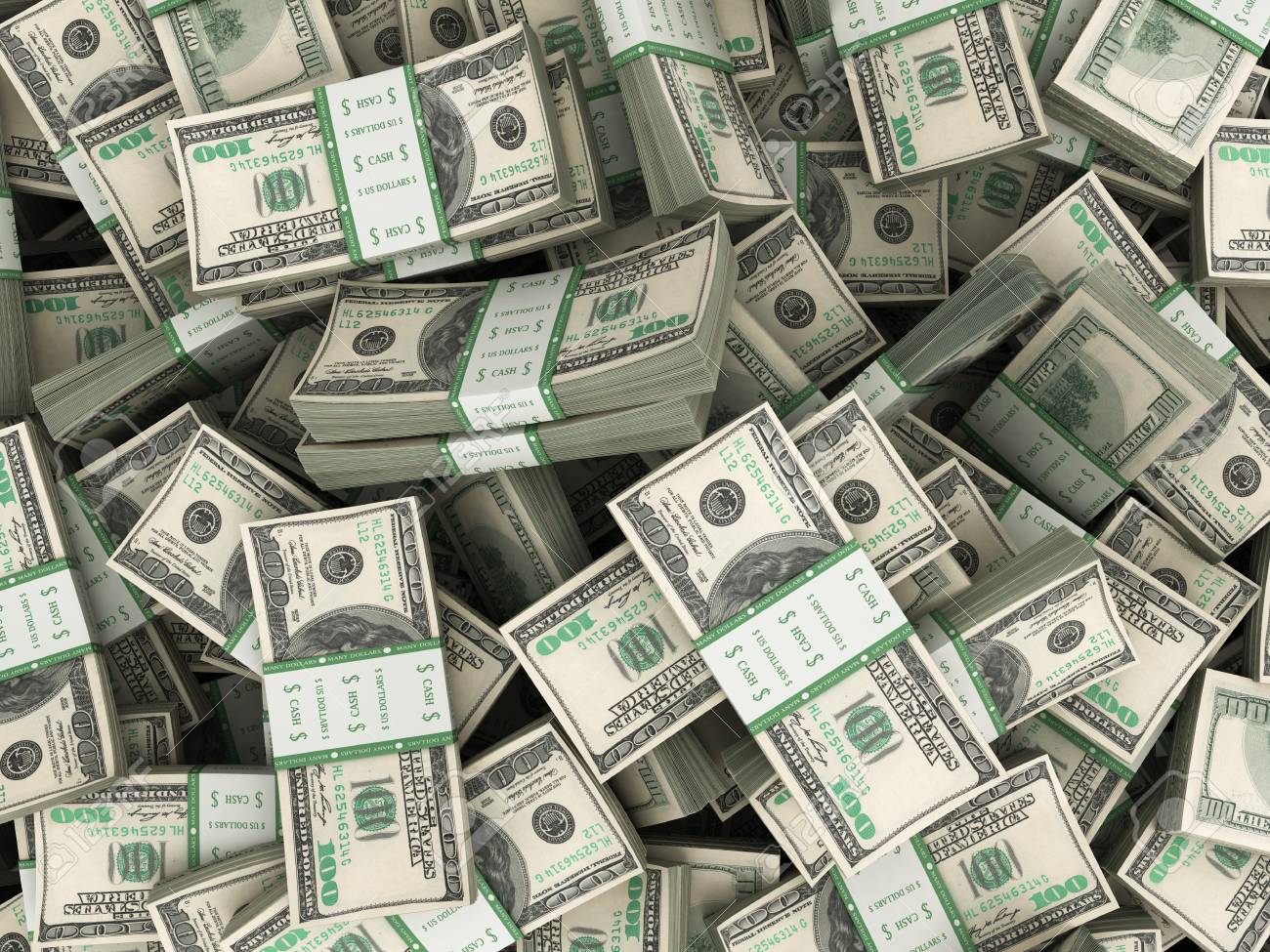
Organizations frequently embark on cost reduction initiatives across their enterprises. Some organizations handle it at the corporate level, while others have Purchasing Departments whose responsibility is to get the right product or service to the right location at the best cost. In either case, one common question always arises – where are the cost savings? Where can I see them? Frustration can occur if visibility is not shed on the challenges inherent in this process.
Most of us would assume that cost savings would be easily identified on the Profit and Loss statement generated each month, right? Wrong!
Why Don’t I See the Savings?
Example: Your organization reduced your office supply pricing by 25% and expect to see average savings of $24,000 per year on office supplies. You have verified that all employees are using the designated supplier at the new prices. So, you’d like to see $24k less on your P&L. However, the office supply spend is blended into a category on your P & L entitled “Supplies” and the spend for “Supplies” this month actually increased…how can that be?
- Blending Problem – Some other category (shop supplies, MRO supplies) which is part of this “Supplies” category may have increased this month, hiding the effect and benefits of the new office supply savings.
- Consumption Problem – While the pricing of office supplies has improved by 25%, perhaps your consumption of those supplies increased.
- Supplier and Mix Problem – While the negotiated pricing is in place for designated items, your employees might be purchasing items not on the core list – maybe they are ordering the brass stapler at $25.00 versus the steel stapler at $5.00.
If any of these scenarios occur, the cost savings you achieved are legitimate but the reporting on the P&L will not show it.
What Elements Impact Overall Cost Savings?
When Purchasing Departments or individuals embark on cost savings initiatives, it is a good idea to understand the many components that have an impact on cost. The following items need to be controlled:
- Category Usage – It is possible that an expense may not be necessary to the organization at all. Eliminating that expense would be an obvious way to reduce the cost.
- Business Requirements – The client defines what is needed vs. what is wanted. Do we really need our waste picked up three times a week when maybe two times will work just fine?
- Pricing – Negotiated pricing that is locked for extended periods of time is the best approach. Long- term pricing is the best way to provide sustainable savings.
- Business Terms – 2% 10 payment terms, freight charges, service levels, etc. should always be negotiated as part of the transaction.
- Item/Service Selection – High usage, least cost items should be the most common purchases and an approval process should be in place to control against higher cost substitutions.
- Preferred Supplier – A Preferred Supplier program should be in place to prevent employees from using suppliers without prenegotiated and locked pricing.
All of the above elements of a purchase will have a material impact on the actual cost savings achieved and provide a much better result than focusing on price alone. Most of the elements can be controlled and delivered through a proven 8 step purchasing process across the organization – this process is detailed in our blog post titled “Preferred Supplier Strategy: Reduce Expenses – Increase Profitability.”
Audits – The Best Way to Validate Cost Savings
So far we have reviewed the spend management elements that will yield long term, sustainable cost savings. But what is the best way to validate cost savings across an organization?
A category audit can be used to validate cost savings in any expense. In our experience, there are four components of a category audit.
The pre-negotiated pricing is right + The Preferred Supplier is used + Consumption levels are correctly realized + The right items are being purchased
If your category audit consists of these four components, rest assured that your savings are there. Even if they are buried in various financials you can’t dispute that prices are lower, terms are better, the spend in that category is lower, and the limited spend dollars are being used with the most cost effective items.
Summary
We started this paper with a question “Where are the cost savings?”
While traditional financial documents such as the P & L fall short, a series of post-implementation audits that focus on price, supplier, and consumption accuracy can validate your savings. When management asks “Where are the Cost Savings?” you can point to your audit results as proof positive that not only are pricing and terms better, but employee behavior and decisions have improved as well. All of this leads to sustainable cost savings today, tomorrow, and into the future.